Out-of-Sequence Progress
Many projects encounter so called “out-of-sequence” progress. This occurs when a following activity has a remaining duration less than its original duration (i.e. some work has been done) without all of its prior activities having a remaining duration equal to zero (i.e. all work has been completed). As you can see from this definition, out-of-sequence progress refers to time- based progress and not earned value progress.
Let’s look at an example project, shown in fenced-bar chart format in the figure below. The project begins and ends each with a single activity. There are two sets of parallel activities that complete the middle of the project. Let’s assume now that we are at working day 10 and we want to determine how much progress has been made.
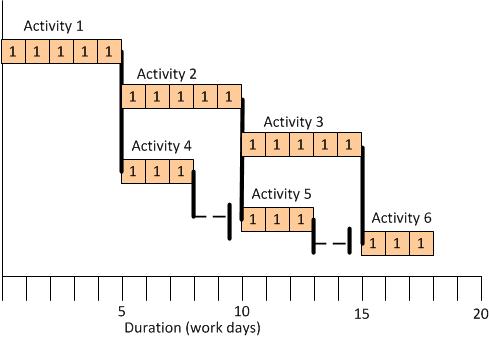
When we talk to the superintendent we find the following progress has been made:
- Activity 1 Remaining Duration = 0
- Activity 2 Remaining Duration = 2
- Activity 3 Remaining Duration = 3
- Activity 4 Remaining Duration = 1
- Activity 5 Remaining Duration = 2
- Activity 6 Remaining Duration = 3
With this progress information we can update the schedule as shown in the figure below. Green shading is used to signify the progress that has been made on Day 10. Looking at the figure you can clearly see the out- of-sequence progress. Activity 3 has begun before the completion of Activity 2. Similarly Activity 5 has started before the completion of Activity 4.
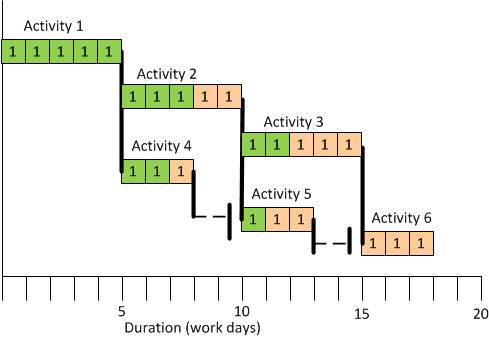
There are two concerns that you might have at this point. The first is that the Critical Path Method model of the project created is incorrect. Since you will often encounter such out-of-sequence progress, the question that we really need to answer is, “When do we get excited enough to update schedule? My answer to this question is that if the out-of-sequence progress will be resolved before the next progress reporting period, then there is no reason to update the model.
In the figure above, for example, if the first progress period was on day 10, the second would be expected to be on day 20. In this trivial example the project will be over by the time the team gets around to changing the schedule. So why bother correcting the schedule. On the other hand, if activities are occurring across more than one progress cycle, then the schedule should be updated. What will be required will be to decompose the long, out-of-sequence activity with at least one (and possibly several) additional task(s).
The next concern that should be addressed with out-of-sequence progress is “How do I schedule the project given that the logic of the schedule is messed up?” To answer this question it is important to consider what part of the logic is incorrect and see if there is also a part that is still correct. The incorrect part of the model’s logic is clearly the constraint on the start of the following activity.
We can assume that the correct part of the logic is that the finish constraints on the end of the activities are still valid. On a horizontal project it is still the case that the pipe cannot be backfilled until the whole reach of piping has been installed As a result, when we calculate the CPM schedule dates we may must consider that the finish constraints still govern.
Knowing how to handle the CPM schedule calculations for our example project allows us to determine, from the figure below, that the project is on schedule with no delays expected. The first thing to note is that all progress, in-sequence or out-of-sequence appears to the left of the red calculation date (or “data date”). The activities shown to the right of the data date are the remaining durations of Activities 2-5, plus Activity 6, which has not yet started.
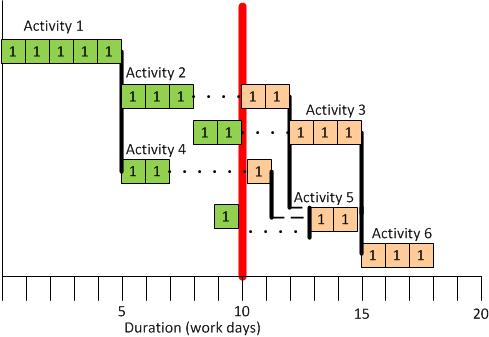
We begin with the first of the out-of-sequence activities and work our way forward. Activity 2 must be completed prior to the start of Activity 3, therefore the finish- to-start constraint between these two activities remains in place on the figure above. You can trace each of the finish constraints on the remaining activities to verify that they are still represented in the schedule.
While the above approach assumes that the underlying CPM model is “mostly” correct and just adjusts the remaining durations of the in-progress schedules within the context of the CPM logic, there are other approaches. One approach is to consider the logic of the out of sequence progress activities to be incurred, and to ignore all out-of-sequence activities’ logic. If this were the case then the example above would show the project being finished on day 13 and not day 18.
As you begin to use your scheduling software there are several tests you should perform. One of these is the out-of-sequence progress test. Consider using the example above in your scheduling software to ensure that the logical connections of remaining out-of-sequence progress are maintained.
Conclusions
So now that you know about out-of-sequence progress, let’s summarize the contents of this page:
- Out-of-sequence progress is a natural consequence of modeling construction
using CPM.
- The CPM can correctly calculate out-of-sequence progress provided that the
finish logic is maintained by the scheduling software.
- Schedules with activities whose durations are no more than that of the
duration of the progress evaluation period, will typically show out-of-sequence
progress for a given activity during one pay period.
- The logic of activities showing out-of-sequence progress for more than one progress period should be revised.
For your consideration….
When might having additional crews lead to out-of-sequence progress?
Are there differences between the types of out-of-sequence progress that might be found on horizontal or vertical projects?
If you have to update the logic to represent long duration activities how would you do it? How would you show that change in ADM? in PDM? Use the example above to assist you.