Production Planning
In the factory production system workers and robots are assigned to specific locations on the factory floor. The work product moves on conveying systems through a variety of work stations where the production resources (workers and robots) to attach pre-manufactured components or assemblies to the in-progress product. At the end of the line, after all components have been attached and the product has been tested, the product is ready for use.
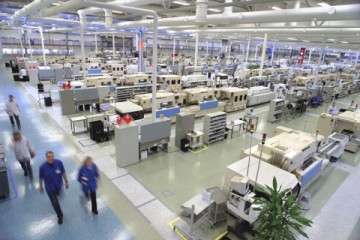
The construction process could also be considered to be a manufacturing process but it is a process that is significantly different from the factory production line. The most important difference is that the product to be manufactured is so large that it must be built from within. The workers move through the product and install pre-manufactured components or assemblies to the building as the finished product grows over time. The analogy between construction and manufacturing is useful from the point of view of tracking work effort through product progress.
Construction Planning
If one thinks about the mid-rise apartment building noted in the picture below in the context of a the work to be accomplished on each floor of the cast-in-place concrete structure, one can come up with an expected list of tasks to be accomplished on each floor. Given that different crew will be responsible for the activities on each floor, consider what might be meant by the term “crew chase.”
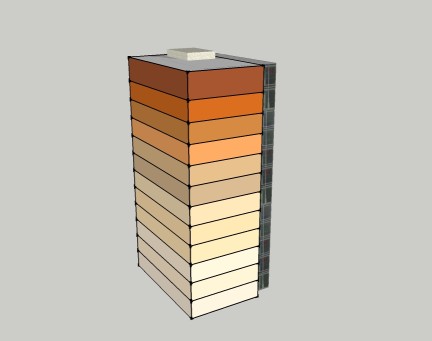
The Crew Chase
In your mental model of how crews would move through the project you might have considered a set of tasks in sequence working through each floor. Such a set of tasks might be the following list: formwork, place concrete, cure concrete, exterior closure, stud walls, rough-in electrical, rough plumbing, HVAC, finish carpentry, finish electrical, finish plumbing, paint, and carpet. With such a template schedule you can prepare a schedule for the majority of the work required to complete this project.
Visualize the steel stud walls being built on the first, then second, then third, and the other floors in sequence. Now after the completion of the steel studs on the first floor, visualize the rough electrical and plumbing being installed. Once the work areas are available, the following crews proceed through each floor.
As you consider the interaction of these crews across work areas you may notice the impact that the differences in the durations of activities have on the timing of crew arrivals. A Line of Balance diagram will be particularly useful to visualize these interactions. If you decompose activities by work area and responsibility, then you will directly able to create the line of balance diagrams from CPM schedule calculations.
Just to be very clear there are two sets of constraints that impact the sequence in our example project. The first constraint is the technical sequence imposed on a given floor that would generally be included in a CPM schedule. The second constraint is the limited resource of workspace keeping the crew from moving into the next work area. Effective schedulers must model the workspace constraint by adding limiting sequential relationships into the schedule and communicate these links reports that show work completion through work areas, by crew.
By defining activities by responsibility you can more easily communicate to members of each subcontractor when they are to arrive and depart from the project in a way that is immediately understood.
There are three techniques that can be used, depending on the scheduling software your team is using, to effectively include crew type into a scheduling tool.
Activity ID Coding
The easiest way to identify activities by crew type in that should work regardless of the software used, is to embed the coding within the Activity ID number. Consider using an Activity ID that is composed of eight characters (which happen to be numbers not letters). The second two positions of the Activity ID can be set to correspond to the crew that is responsible for the work to be accomplished. Given two example activities from an arbitrary schedule, such as “10110239” and “20110239,” without knowing anything about the actual work to be accomplished you can immediately infer that both activities are the responsibility of crew “11.” Since most scheduling systems have report writers that allow the selection of specific activities, getting a report of all activities with a given crew should be no problem.
Responsibility Coding
The Responsibility Code directly allows a high-level, but extremely practical and useful, evaluation of crew productivity. Reports using the “Work Area” and “Responsibility Code” provide the scheduler with tools to assist superintendant and subcontractors identify the number of workers that would be optimal to send to the project and potential inefficient resource allocations. While a full resource leveling effort could be done, the schedule can, with some assumptions about the number of crews that need to be allocated, approximate the leveling using actual dates from the schedule.
Note that the Responsibility Code is not a formal resource loading that is possible in most scheduling systems. Given the discrete nature of crew formation and the general repetitive patterns of work occurring on the majority of commercial construction projects, such resource analysis may not be as productive as using the Work Area and Responsibility Code.
Activity Coding Lessons Learned
The coding schema for the whole project must be fully defined prior to the entry of a single activity. If activities are entered first and then the activity coding scheme is developed, then the scheduler will have to edit every activity in the schedule. Entering the coding scheme when the activities are created takes a lot less time. Please consider this a “lessons learned” from me to you.
Hammock Activities
A way to group activities that pertain to specific crew types is to use a "hammock" activity. The time to complete hammock activities depends on the starting and ending activities in the sequence of tasks to which the hammock is linked. The hammock activity, by definition, has no duration of its own and does not impact schedule calculation in any way. Link your hammock activity, one per crew, to the start of the first activity requiring a given crew type. Complete the hammock by linking the end of the activity with the end of the last activity that occurs for that crew type.